Extruder screens are engineered to withstand high temperatures, corrosive environments, and intense pressure, making them indispensable in various manufacturing sectors such as plastics, rubber, food processing, pharmaceuticals, and more. Their intricate design, characterized by precise mesh patterns and durable construction, enables them to effectively trap contaminants like debris, metal particles, or oversized chunks that could compromise the integrity of the final product or damage the extruder machinery.
Mesh Tech (India) distinguishes itself through its commitment to innovation and customization. Beyond offering standard extruder screen sizes and configurations, Mesh Tech (India) collaborates closely with clients to develop tailored solutions that address specific operational challenges and enhance efficiency. Whether it’s optimizing mesh density, adjusting pore sizes, or exploring alternative materials, Mesh Tech (India) leverages cutting-edge technologies and extensive industry expertise to deliver superior products that meet or exceed client expectations.
Moreover, Mesh Tech (India) prioritizes sustainability and eco-friendliness in its manufacturing processes. By employing advanced techniques like precision laser cutting and automated welding, the company minimizes material wastage and energy consumption while maximizing product consistency and reliability. Additionally, Mesh Tech (India) is committed to recyclability, ensuring that its extruder screens can be responsibly disposed of or repurposed at the end of their lifecycle, thereby reducing environmental impact.
Furthermore, Mesh Tech (India) places a strong emphasis on quality assurance and rigorous testing protocols. Each extruder screen undergoes meticulous inspection and performance evaluation to verify dimensional accuracy, structural integrity, and filtration efficiency. By adhering to stringent quality standards and continuous improvement initiatives, Mesh Tech (India) instills confidence in its clientele, fostering long-term partnerships built on trust and reliability.
In essence, extruder screens may be small in size, but their significance in manufacturing processes cannot be overstated. As guardians of product purity and machinery integrity, these screens play a vital role in ensuring operational excellence and product excellence. Mesh Tech (India) emerges as a beacon of innovation and excellence in this realm, pioneering advancements that elevate industry standards and empower businesses to thrive in an ever-evolving landscape of manufacturing.
The Purpose They Serve:
Contaminant Removal: Extruder screens act as the first line of defense against contaminants such as dust, metal particles, and other debris present in the raw materials or introduced during the manufacturing process. By capturing these impurities, they prevent them from entering the extrusion die and potentially causing defects in the product.
Pressure Regulation: In extrusion processes, maintaining consistent pressure is crucial for achieving uniform product dimensions and properties. Extruder screens help regulate pressure by evenly distributing the material flow, minimizing fluctuations that could result in irregularities or product defects.
Enhanced Product Quality: By removing impurities and ensuring uniform flow, extruder screens contribute to the overall quality and aesthetics of the final product. Whether it’s plastic pellets, food products, or pharmaceutical formulations, the use of extruder screens helps meet stringent quality standards and customer expectations.
Types of Extruder Screens:
Extruder screens come in various types and configurations to suit different manufacturing requirements. Some common types include:
Wire Mesh Screens: These screens consist of woven wire mesh with precise mesh openings tailored to the application’s filtration needs. They offer excellent durability and are suitable for a wide range of materials and operating conditions.
Sintered Metal Filters: Made from metal powders that are sintered together, these filters provide superior strength and resistance to high temperatures and corrosion. They are ideal for demanding applications where durability and longevity are paramount.
Perforated Plates: Constructed from flat metal sheets with uniformly spaced perforations, perforated plates offer effective filtration while allowing for higher flow rates compared to wire mesh screens. They are commonly used in processes requiring coarse filtration.
Importance in Manufacturing Efficiency:
The significance of extruder screens in enhancing manufacturing efficiency cannot be overstated. Here’s how they contribute to streamlined operations:
Minimized Downtime: By preventing contaminants from entering the extrusion system, extruder screens help minimize downtime associated with equipment maintenance, cleaning, and repairs. This translates to increased productivity and optimized production schedules.
Consistent Product Quality: Maintaining consistent filtration ensures that the final product meets quality standards batch after batch. This reduces waste, rework, and rejects, ultimately improving overall efficiency and profitability.
Extended Equipment Lifespan: Extruder screens protect downstream equipment such as dies, molds, and nozzles from damage caused by contaminants. By safeguarding these critical components, they contribute to extending the lifespan of expensive equipment and reducing replacement costs.
Compliance and Safety: In industries such as food processing and pharmaceuticals, adherence to regulatory standards and product safety requirements is non-negotiable. Extruder screens help ensure compliance by removing contaminants that could compromise product integrity or pose safety risks to consumers.
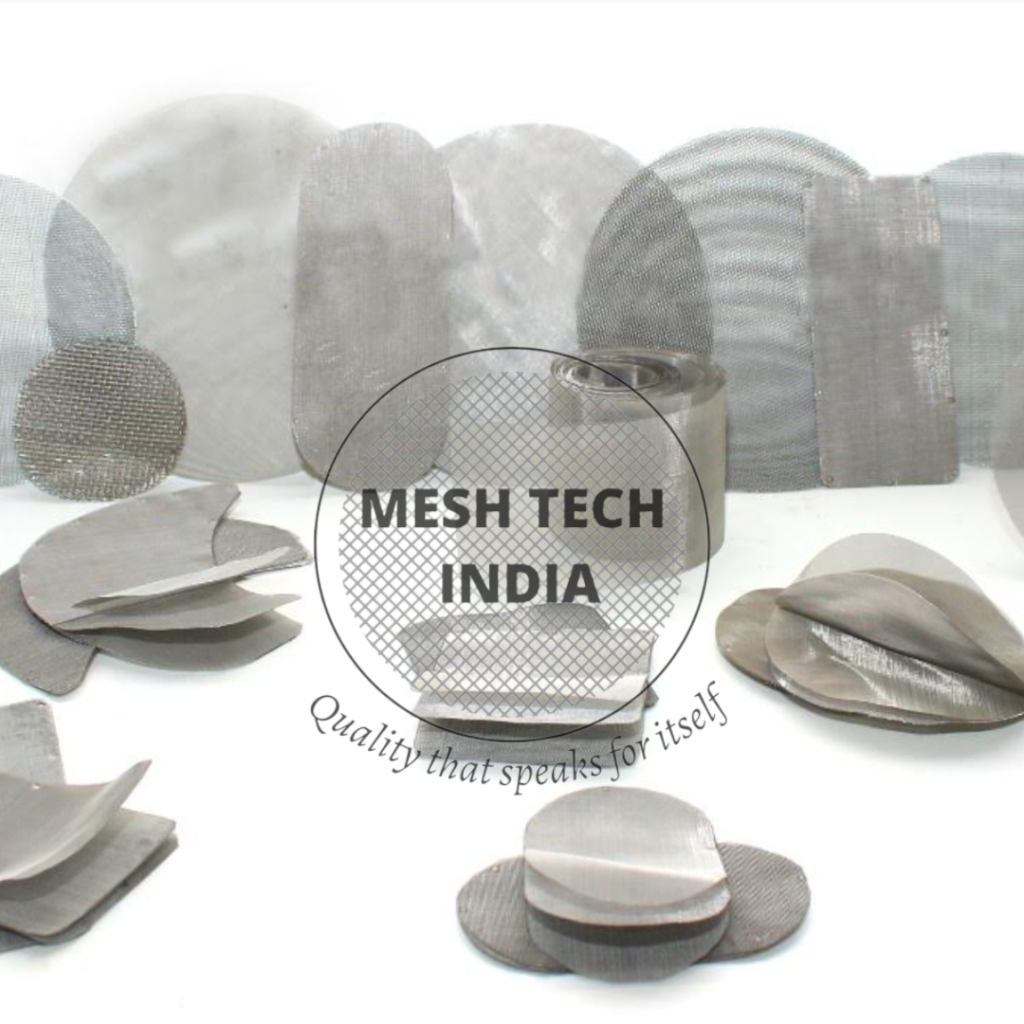
The Role of Extruder Screens:
Embedded within manufacturing processes, extruder screens from Mesh Tech (India) play a multifaceted role, contributing to:
Quality Control: Mesh Tech (India)’s extruder screens are instrumental in maintaining product purity and consistency. By eliminating contaminants, they uphold stringent industry standards, bolstering consumer trust in the final products.
Equipment Protection: Industrial machinery, including extruders, is susceptible to damage from foreign particles. Mesh Tech (India)’s screens act as a protective barrier, safeguarding equipment integrity and reducing maintenance expenditures.
Process Efficiency: Seamless material flow is pivotal for operational efficiency. Mesh Tech (India)’s meticulously engineered screens ensure uninterrupted production, optimizing output and minimizing downtime.
Versatility: Mesh Tech (India)’s extruder screens find applications across diverse industries, from plastics to food processing, owing to their adaptability and reliability.
Mesh Tech (India) Leading the Way: In a fiercely competitive landscape, Mesh Tech (India) emerges as a beacon of excellence, characterized by:
Innovative Solutions: Mesh Tech (India) continually pioneers advancements in extruder screen technology, delivering innovative solutions tailored to the evolving needs of industries.
Uncompromising Quality: With a steadfast commitment to excellence, Mesh Tech (India) upholds the highest quality standards in every product, ensuring durability, reliability, and performance.
Customer-Centric Approach: Mesh Tech (India) places customer satisfaction at the forefront, offering personalized solutions and exemplary support to clients worldwide.
Global Reach: Mesh Tech (India)’s footprint extends far beyond borders, serving industries across the globe and earning acclaim for its unparalleled expertise and reliability.
Additional Points:
Customization Options: Mesh Tech (India) offers a wide range of customization options for extruder screens, catering to specific requirements of different manufacturing processes. This flexibility ensures optimal performance and compatibility with diverse materials and production conditions.
Continuous Improvement: Mesh Tech (India) is committed to continuous improvement in its products and processes. Through rigorous research and development efforts, they stay at the forefront of technological advancements, constantly refining their extruder screens to meet the evolving demands of the industry.
Environmental Sustainability: Mesh Tech (India) integrates eco-friendly practices into its manufacturing processes, ensuring that its extruder screens contribute to sustainable production. By reducing waste and energy consumption, Mesh Tech (India) helps clients minimize their environmental footprint while maintaining high standards of productivity.
Technical Expertise: Mesh Tech (India) boasts a team of highly skilled engineers and technicians who possess deep expertise in extruder screen design, manufacturing, and application. This technical proficiency enables Mesh Tech (India) to provide comprehensive support to clients, including troubleshooting, optimization, and customization services.
Collaborative Partnerships: Mesh Tech (India) fosters collaborative partnerships with clients, suppliers, and industry stakeholders to drive innovation and mutual success. By actively engaging with customers and seeking their feedback, Mesh Tech (India) ensures that its extruder screens are finely tuned to meet the dynamic needs of the market.
Compliance and Regulation: Mesh Tech (India) adheres to all relevant industry regulations and standards, ensuring that its extruder screens meet the highest levels of safety and performance. These certifications provide assurance to clients of Mesh Tech (India)’s commitment to excellence and continuous improvement.
Training and Education: Mesh Tech (India) offers training programs and educational resources to help clients optimize their use of extruder screens. By empowering customers with knowledge and skills, Mesh Tech (India) enhances the effectiveness and efficiency of their production operations, fostering long-term partnerships built on trust and mutual success.
Cost Efficiency: By preventing equipment downtime and minimizing material wastage, Mesh Tech (India)’s extruder screens contribute to significant cost savings for manufacturers. The long lifespan and durability of these screens further enhance their cost efficiency over time.
Conclusion
In the intricate tapestry of manufacturing, extruder screens stand as unsung heroes, diligently ensuring the purity and quality of our everyday products. Mesh Tech (India) emerges as a luminary within this domain, not merely as a supplier but as a partner in innovation and progress. With an unwavering commitment to excellence, Mesh Tech continuously pushes boundaries, pioneering new frontiers, and setting benchmarks for others to follow.
As industries evolve and demand for precision manufacturing grows, Mesh Tech’s dedication to innovation and customer satisfaction ensures that the future of extruder screens shines brighter than ever before, promising a world of cleaner, safer, and more efficient production processes. Mesh Tech’s relentless pursuit of excellence has transformed it from a mere supplier of extruder screens to a trailblazer in the field, driving the industry forward and inspiring confidence in the capabilities of modern manufacturing.
In Mesh Tech (India), we find not just a provider of extruder screens, but a catalyst for transformative change. Their commitment to advancing manufacturing technology extends beyond the confines of their facilities, embodying the spirit of innovation and collaboration that fuels progress across industries. With each screen they produce, Mesh Tech reinforces its dedication to shaping the future of manufacturing, fostering a culture of excellence and reliability that resonates throughout the global market.
Looking ahead, Mesh Tech (India) stands poised to continue leading the charge, leveraging its expertise and ingenuity to address the evolving needs of industries worldwide. Their legacy of innovation and commitment to customer satisfaction ensures that they will remain at the forefront of extruder screen technology, paving the way for a more sustainable, efficient, and prosperous future for manufacturing on a global scale. As we embark on this journey of progress, Mesh Tech (India) serves as a beacon of hope and inspiration, guiding us towards a brighter tomorrow built on the foundation of excellence and innovation.