Introduction to Wire Mesh
Wire mesh, a versatile material used across various industries, owes its functionality to the intricate weaving patterns that give it structure and strength. Over the past two decades, the manufacturing process of wire mesh has evolved significantly, thanks to advancements in automation and programming. These innovations have not only improved the efficiency of production but also enhanced the quality and reliability of wire mesh products.
The Importance of Weaving Patterns
One of the fundamental aspects of wire mesh production is the weaving pattern employed during manufacturing. Weaving patterns dictate the arrangement of horizontal (weft) and vertical (warp) wires, as well as the thickness of these wires, ultimately determining the characteristics and performance of the wire mesh. Let’s delve into some of the most common weaving patterns and their unique features:
Plain Weave Pattern
The plain weave pattern is perhaps the most ubiquitous and straightforward weaving pattern used in wire mesh production. In this pattern, each horizontal weft wire passes alternately over and under each vertical warp wire at a 90-degree angle. The result is a uniform grid-like structure with square-shaped apertures.
One of the defining characteristics of the plain weave pattern is its simplicity. Both the weft and warp wires have the same diameter, contributing to a balanced and symmetrical mesh. This pattern is versatile and finds applications across a wide range of industries, from filtration and screening to reinforcement and partitioning.
Despite its widespread use, the plain weave pattern does have its limitations. Its relatively simple structure means that it offers less strength compared to more complex weaving patterns.
Plain Dutch Weave Pattern
The Plain Dutch weave pattern shares similarities with the plain weave but differs in the wire diameter used for weaving. In this pattern, fine horizontal weft wires are paired with relatively coarser vertical warp wires. The result is a mesh with a tighter weave and finer apertures compared to the plain weave.
The Plain Dutch weave pattern offers enhanced rigidity and durability, making it suitable for applications where finer filtration and increased strength are required. Additionally, the combination of fine and coarse wires enables the mesh to retain particles more effectively while maintaining structural integrity.
This pattern finds applications in industries such as chemical processing, oil and gas, and aerospace, where precise filtration and robust performance are essential.
Twilled Weave Pattern
The twilled weave pattern introduces a more complex weaving technique compared to the plain weave. In this pattern, each vertical warp wire alternately passes over and under two horizontal weft wires in a diagonal fashion. This results in a distinctive diagonal pattern across the surface of the mesh.
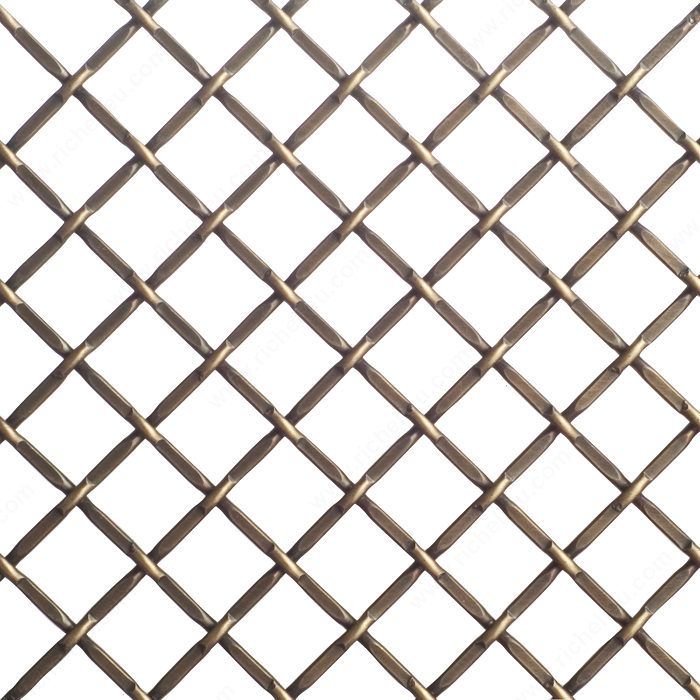
One of the key advantages of the twilled weave pattern is its ability to accommodate heavier wires, making it suitable for weaving heavy-duty meshes with increased strength and durability. This pattern is often used in applications where greater mechanical stability and load-bearing capacity are required, such as industrial sieving and screening.
Despite its enhanced strength, the twilled weave pattern may have slightly larger apertures compared to plain or plain Dutch weave patterns.
Dutch Twilled Weave Pattern
The Dutch twilled weave pattern combines elements of both the twilled weave and plain Dutch weave patterns. In this pattern, the weft wires are finer in diameter compared to the warp wires, resulting in a mesh with larger wire diameters and increased rigidity.
This weaving pattern is known for its exceptional strength and stability, making it suitable for demanding applications where superior mechanical performance is required. The Dutch twilled weave pattern is often used in industries such as mining, construction, and automotive manufacturing, where robust and reliable wire mesh solutions are essential.
Conclusion
In summary, wire mesh weaving patterns play a crucial role in determining the characteristics and performance of wire mesh products. From the simplicity of the plain weave pattern to the enhanced strength of the Dutch twilled weave pattern, each weaving pattern offers unique features suited to specific applications. By understanding these weaving patterns, manufacturers and end-users can select the most suitable wire mesh for their respective need